You undoubtedly know that marine fenders, or rubber fenders, are crucial for ensuring safe and gentle mooring of ships, protecting both ship and marine structures from damage. But did you know that the safety valve in air-filled fenders is a necessity in maintaining their functionality and lifespan?
The safety valve, often referred to as a ‘pressure safety valve’ (PSV), is a critical component that safeguards your fender from excessive pressure and the potential hazardous consequences thereof.
In this article, we will explore how to maintain the safety valve on your fender products to ensure the best possible performance and safety.
The Critical Role of the Safety Valve
What Is a Safety Valve and Why Is It Essential?
A safety valve plays a key role in controlling the pressure in a fender filled with air. Think of it as an overpressure valve that protects the fender from the potentially catastrophic effects of high pressure. Overpressure can cause the fender to rupture or in worst case scenarios, explode.
The safety valve’s task is to release air when pressure inside the fender exceeds a safe level, typically around 1.75 bar. This prevents overpressure and reduces the risk of the fender rupturing or exploding under extreme conditions. Many might not be aware, but for fender sizes larger than 250 cm in in diameter, such a valve is obligatory according to ISO-standards.
Maintenance and Monitoring of the Safety Valve
To preserve the fender’s safety and efficiency, regular maintenance of the safety valve is recommended every two years. The process includes deflating the fenders, removing and then calibrating the valve. Calibration ensures that the valve opens at the correct pressure and should be performed in a controlled environment, often requiring a test bench.
After calibration, it is essential to replace worn parts like gasket seals to ensure the valve remains air-tight and functions correctly. This is crucial, as worn gaskets can lead to leaks that affect the fender’s efficiency and safety.
In some cases, the valve’s wear and corrosion can be too severe to preserve it. If so, replacing the entire valve can be more appropriate to ensure optimal function.
By maintaining the safety valves, you ensure your fender is not exposed to overpressure that could lead to damage or failure. This is a crucial part of the fender’s overall maintenance program and must not be overlooked.
Who Should Do What?
A basic rule of thumb is that while some maintenance tasks can be performed independently, calibration and gasket replacement often require specialised expertise. For example, deflating the fender of air and removing the safety valve can be performed by personnel with basic training, but calibration requires technical expertise and specialised equipment. It is also important to note that there is a significant difference in safety valves from different manufacturers. Some valves are nearly impossible to calibrate, making it crucial to be informed about the type of valve when purchasing a fender.
Takeaway:
Maintenance of the safety valve on a fender is not only routine maintenance; it is a critical part of the fender’s safety and effectiveness. Regular monitoring, calibration and maintenance of the safety valve, coupled with a careful assessment of the fender’s condition and any repair or replacement needs, are vital to ensuring that marine fender systems operate reliably and safely over the long term. Remember, it is not just a matter of maintenance but also safety. So, set up a maintenance plan, know your fender’s specifications and do not hesitate to seek professional help when necessary.
Understanding and implementing these maintenance strategies are essential when protecting valuable maritime assets and infrastructures against inevitable impacts that come with maritime operations.
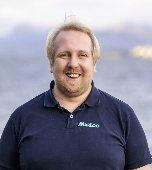